مشکل شفافیت در پلیمرها؟ با این افزودنی ها مشکل را برطرف کنید
چگونه مشکل شفافیت در پلیمرها را با افزودنی ها حل کنیم؟
شفافیت یکی از ویژگی های حیاتی و مطلوب در بسیاری از محصولات پلیمری است از بسته بندی مواد غذایی و دارویی گرفته تا لنزها شیشه های خودرو و تجهیزات پزشکی. با این حال دستیابی به شفافیت کامل و حفظ آن در طول فرآیند تولید و عمر مفید محصول چالش های متعددی را برای تولیدکنندگان به همراه دارد.
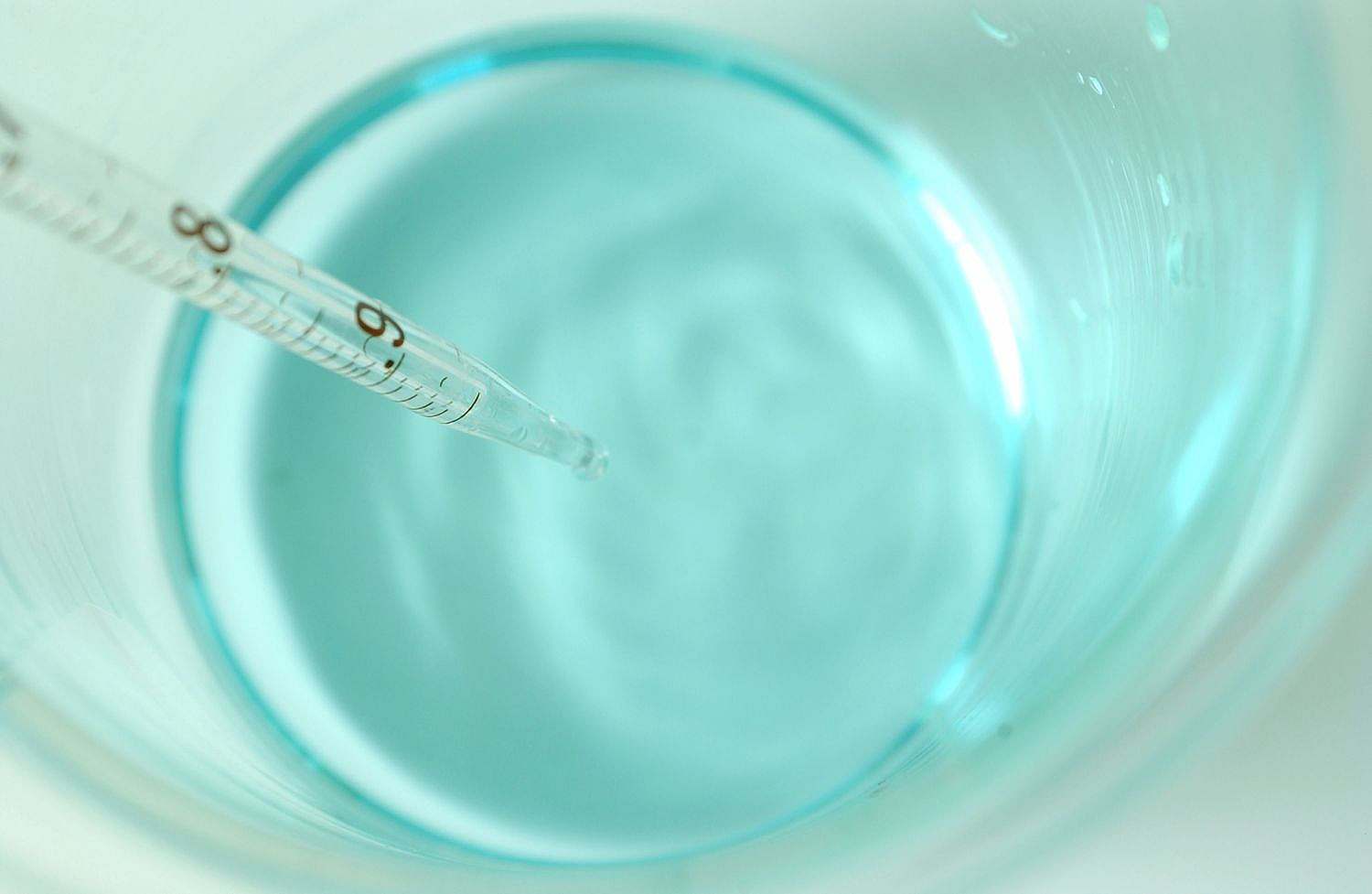
کدورت یا کاهش شفافیت می تواند به دلایل گوناگونی رخ دهد و بر کیفیت ظاهری و عملکردی محصول تاثیر منفی بگذارد. درک این عوامل و شناخت راهکارهای موثر برای رفع آن ها کلید تولید محصولاتی با شفافیت بالا و مطابق با استانداردهای مورد نیاز بازار است. در این مقاله به بررسی عمیق دلایل کاهش شفافیت در پلیمرها و معرفی جامع انواع افزودنی های بهبود دهنده شفافیت می پردازیم و نکات کاربردی برای انتخاب و استفاده صحیح از این مواد ارائه خواهیم داد. هدف ما ارائه یک راهنمای تخصصی برای فعالان صنعت پلیمر است تا بتوانند با دانش کافی به چالش شفافیت غلبه کرده و مزیت رقابتی خود را افزایش دهند.
چرا پلیمرها شفافیت خود را از دست می دهند؟
شفافیت یک ماده پلیمری به توانایی آن در عبور نور مرئی بدون پراکندگی قابل توجه بستگی دارد. هر عاملی که باعث پراکندگی یا جذب ناخواسته نور در ساختار پلیمر شود می تواند شفافیت را کاهش داده و منجر به کدورت شود. این عوامل ریشه در ساختار شیمیایی فرآیند تولید و ترکیب نهایی پلیمر دارند.
شناخت دقیق مکانیسم هایی که باعث کاهش شفافیت می شوند اولین گام در انتخاب راه حل مناسب برای رفع این مشکل است. در ادامه به بررسی مهم ترین این عوامل می پردازیم.
ناسازگاری اجزا و تاثیر آن بر شفافیت
پلیمرها اغلب به تنهایی استفاده نمی شوند بلکه با افزودنی های مختلف (مانند پایدارکننده ها رنگدانه ها پرکننده ها) یا حتی با پلیمرهای دیگر (در آلیاژها و مخلوط های پلیمری) ترکیب می شوند. اگر این اجزای مختلف با یکدیگر سازگاری نداشته باشند تمایل به جدایی فازی پیدا می کنند.
تشکیل فازهای جداگانه در مقیاس میکروسکوپی باعث ایجاد مرزهای فازی می شود. هرگاه نور از یک فاز با ضریب شکست مشخص به فاز دیگری با ضریب شکست متفاوت عبور کند در این مرزها دچار پراکندگی می شود. این پراکندگی نور همان چیزی است که ما به صورت کدورت یا ماتی مشاهده می کنیم. شدت کدورت به میزان ناسازگاری اندازه فازهای جدا شده و اختلاف ضریب شکست بین فازها بستگی دارد.
نقش ناخالصی ها در کدورت پلیمرها
حضور ناخالصی ها در ماده اولیه پلیمری یا آلودگی های وارد شده در حین فرآیند تولید نیز یکی از دلایل اصلی کاهش شفافیت است. این ناخالصی ها می توانند ذرات جامد (مانند گرد و غبار باقی مانده کاتالیست یا ذرات خارجی) مایعات نامحلول یا حتی حباب های گاز باشند.
این ذرات ناخالص همانند فازهای جدا شده در اثر ناسازگاری باعث پراکندگی نور می شوند. اندازه شکل غلظت و ضریب شکست ناخالصی ها نسبت به پلیمر پایه همگی بر میزان کدورت تاثیرگذارند. حتی مقادیر بسیار کم ناخالصی می تواند شفافیت محصول نهایی را به شدت کاهش دهد.
کریستالیزاسیون و تاثیر آن بر شفافیت
برخی از پلیمرها مانند پلی پروپیلن (PP) پلی اتیلن (PE) و پلی اتیلن ترفتالات (PET) قابلیت تشکیل ساختارهای کریستالی را دارند. در پلیمرهای نیمه کریستالی هم نواحی کریستالی منظم و هم نواحی آمورف (بی شکل) نامنظم وجود دارند.
نواحی کریستالی دارای چگالی و نظم مولکولی متفاوتی نسبت به نواحی آمورف هستند که منجر به اختلاف در ضریب شکست می شود. این اختلاف ضریب شکست در مرز بین نواحی کریستالی و آمورف باعث پراکندگی نور می شود. اندازه و تعداد کریستال ها (یا به عبارت دقیق تر اسفرولیت ها که مجموعه های کروی از لایه های کریستالی هستند) تاثیر مستقیمی بر شفافیت دارد. کریستال های بزرگتر نور را بیشتر پراکنده می کنند و باعث کدورت بیشتری می شوند. بنابراین کنترل فرآیند کریستالیزاسیون برای دستیابی به شفافیت بالا در پلیمرهای نیمه کریستالی بسیار حیاتی است.
تخریب حرارتی و نوری و تاثیر آن ها بر شفافیت
پلیمرها ممکن است در طول فرآیند تولید (تحت دما و تنش بالا) یا در طول عمر مفید محصول (در معرض نور خورشید حرارت یا مواد شیمیایی) دچار تخریب شوند. تخریب پلیمری معمولاً با شکسته شدن زنجیره های پلیمری تشکیل رادیکال های آزاد و ایجاد تغییرات شیمیایی در ساختار همراه است.
یکی از پیامدهای رایج تخریب تغییر رنگ پلیمر است که اغلب به صورت زرد شدن ظاهر می شود. این تغییر رنگ به دلیل تشکیل کروموفورها (گروه های شیمیایی جذب کننده نور مرئی) رخ می دهد و باعث جذب بخشی از نور عبوری و کاهش شفافیت و وضوح تصویر می شود. علاوه بر این تخریب می تواند منجر به تشکیل محصولات جانبی فرار یا نامحلول شود که خود به عنوان ناخالصی عمل کرده و باعث کدورت می شوند.
انواع افزودنی های بهبود دهنده شفافیت پلیمرها
صنعت پلیمر برای مقابله با چالش های کاهش شفافیت مجموعه ای متنوع از افزودنی های تخصصی را توسعه داده است. این افزودنی ها با مکانیسم های مختلفی عمل می کنند تا پراکندگی نور را کاهش داده یا از ایجاد عواملی که منجر به کدورت می شوند جلوگیری کنند. انتخاب افزودنی مناسب به نوع پلیمر دلیل اصلی کاهش شفافیت فرآیند تولید و کاربرد نهایی محصول بستگی دارد.
در این بخش به معرفی و بررسی رایج ترین دسته های افزودنی های بهبود دهنده شفافیت و نحوه عملکرد آن ها می پردازیم:
شفاف کننده ها (Clarifiers) و مکانیسم عملکرد آن ها
شفاف کننده ها که گاهی هسته زاهای شفاف کننده نیز نامیده می شوند اصلی ترین دسته افزودنی هایی هستند که برای بهبود شفافیت در پلیمرهای نیمه کریستالی به ویژه پلی پروپیلن (PP) و پلی اتیلن (PE) به کار می روند. مکانیسم اصلی عملکرد شفاف کننده ها کنترل فرآیند کریستالیزاسیون است.
این افزودنی ها به عنوان مراکز هسته زایی برای تشکیل کریستال های پلیمری عمل می کنند. با افزودن شفاف کننده تعداد زیادی مرکز هسته زایی در سراسر مذاب پلیمری ایجاد می شود. این امر باعث می شود که کریستالیزاسیون به جای تشکیل تعداد کمی اسفرولیت بزرگ منجر به تشکیل تعداد بسیار زیادی اسفرولیت بسیار کوچک شود. اندازه این اسفرولیت های کوچک (که معمولاً در حد نانومتر یا کمتر از طول موج نور مرئی هستند) به قدری کاهش می یابد که پراکندگی نور در مرزهای کریستالی-آمورف به حداقل می رسد و در نتیجه شفافیت به طور قابل توجهی افزایش می یابد.
انواع مختلفی از شفاف کننده ها وجود دارند که از رایج ترین آن ها می توان به موارد زیر اشاره کرد:
- مشتقات سوربیتول (Sorbitol Derivatives): مانند دی بنزیلیدن سوربیتول (DBS) و مشتقات نسل جدیدتر آن. این ها از جمله موثرترین شفاف کننده ها برای PP هستند و شفافیت بسیار بالایی ایجاد می کنند.
- مواد معدنی هسته زا (Mineral Nucleators): مانند تالک (Talc) یا کائولین (Kaolin). این مواد نیز می توانند به عنوان هسته زا عمل کنند اما معمولاً به اندازه مشتقات سوربیتول شفافیت را افزایش نمی دهند و بیشتر به عنوان عوامل هسته زای عمومی برای کنترل اندازه گویچه های کروی و بهبود سرعت فرآیند استفاده می شوند.
- هسته زاهای پلیمری (Polymeric Nucleators): برخی پلیمرهای خاص یا کوپلیمرها نیز می توانند به عنوان هسته زا عمل کنند.
انتخاب نوع شفاف کننده به نوع پلیمر دمای فرآیند الزامات شفافیت و هزینه ها بستگی دارد. شفاف کننده های مشتق سوربیتول معمولاً بالاترین سطح شفافیت را ارائه می دهند.
نرم کننده ها (Plasticizers) و نقش آن ها در افزایش شفافیت
نرم کننده ها موادی هستند که به پلیمرها اضافه می شوند تا انعطاف پذیری نرمی و قابلیت فرآیندپذیری آن ها را افزایش دهند. مکانیسم اصلی عمل نرم کننده ها کاهش نیروهای بین مولکولی بین زنجیره های پلیمری است.
در برخی موارد به خصوص در پلیمرهای آمورف مانند پلی وینیل کلراید (PVC) افزودن نرم کننده می تواند به بهبود شفافیت نیز کمک کند. چگونه؟
- افزایش سازگاری: نرم کننده ها می توانند به بهبود سازگاری بین اجزای مختلف فرمولاسیون (پلیمر سایر افزودنی ها) کمک کنند و از تشکیل فازهای جداگانه که باعث پراکندگی نور می شوند جلوگیری نمایند.
- کاهش دمای انتقال شیشه ای (Tg): با کاهش Tg پلیمر در دماهای پایین تر انعطاف پذیرتر می شود. این امر می تواند به کاهش تنش های داخلی و بهبود یکنواختی ساختار کمک کند که به نوبه خود می تواند پراکندگی نور را کاهش دهد.
- کاهش ویسکوزیته مذاب: نرم کننده ها ویسکوزیته مذاب را کاهش می دهند و به توزیع یکنواخت سایر افزودنی ها و حذف حباب های هوا کمک می کنند که هر دو می توانند شفافیت را تحت تاثیر قرار دهند.
لازم به ذکر است که نقش اصلی نرم کننده ها افزایش انعطاف پذیری است و بهبود شفافیت یک اثر جانبی مفید در برخی کاربردها و پلیمرها (مانند PVC شفاف) محسوب می شود. انتخاب نرم کننده مناسب نیازمند توجه به سازگاری آن با پلیمر سمیت فراریت و پایداری در طول زمان است.
آنتی اکسیدان ها (Antioxidants) و جلوگیری از تخریب حرارتی
همانطور که پیشتر اشاره شد تخریب حرارتی و اکسیداتیو می تواند منجر به تغییر رنگ و کاهش شفافیت پلیمرها شود. آنتی اکسیدان ها افزودنی هایی هستند که برای جلوگیری یا کاهش سرعت این فرآیندهای تخریبی به کار می روند.
آنتی اکسیدان ها با مهار رادیکال های آزاد و یا تجزیه هیدروپراکسیدها (محصولات میانی واکنش اکسیداسیون) چرخه تخریب پلیمری را متوقف می کنند. با جلوگیری از تشکیل ترکیبات رنگی (کروموفورها) ناشی از تخریب آنتی اکسیدان ها به حفظ شفافیت اولیه پلیمر در طول فرآیند تولید و همچنین در حین قرار گرفتن در معرض حرارت و نور در طول عمر محصول کمک شایانی می کنند.
آنتی اکسیدان ها معمولاً به دو دسته اصلی تقسیم می شوند:
- آنتی اکسیدان های اولیه (Primary Antioxidants): مانند فنل های hindered یا آمین ها. این مواد با رادیکال های آزاد واکنش داده و آن ها را غیرفعال می کنند.
- آنتی اکسیدان های ثانویه (Secondary Antioxidants): مانند فسفیت ها یا تیواسترها. این مواد هیدروپراکسیدها را به محصولات غیرفعال تبدیل می کنند.
در بسیاری از فرمولاسیون های پلیمری ترکیبی از آنتی اکسیدان های اولیه و ثانویه برای دستیابی به حداکثر پایداری در برابر تخریب و حفظ شفافیت به کار می رود.
دیگر افزودنی های موثر بر شفافیت
علاوه بر دسته های اصلی شفاف کننده ها نرم کننده ها و آنتی اکسیدان ها افزودنی های دیگری نیز وجود دارند که می توانند به صورت مستقیم یا غیرمستقیم بر شفافیت پلیمرها تاثیرگذار باشند:
- پایدارکننده های UV (UV Stabilizers): این افزودنی ها با جذب یا مسدود کردن اشعه ماوراء بنفش از تخریب نوری پلیمر جلوگیری می کنند. تخریب نوری نیز می تواند منجر به زرد شدن و کاهش شفافیت شود بنابراین پایدارکننده های UV برای کاربردهای بیرونی و محصولاتی که در معرض نور خورشید قرار دارند حیاتی هستند.
- عوامل سازگارکننده (Compatibilizers): در مخلوط های پلیمری (Blends) که دو یا چند پلیمر ناسازگار با هم ترکیب می شوند عوامل سازگارکننده به بهبود چسبندگی بین فازها و کاهش اندازه فازهای جدا شده کمک می کنند. این امر به طور مستقیم پراکندگی نور را کاهش داده و شفافیت مخلوط را افزایش می دهد.
- عوامل فرآیند (Processing Aids): برخی افزودنی ها فرآیندپذیری پلیمر را بهبود می بخشند مانند کاهش ویسکوزیته مذاب یا بهبود جریان. این می تواند به کاهش تنش ها حذف حباب های هوا و بهبود توزیع یکنواخت سایر افزودنی ها کمک کند که همگی می توانند به شفافیت نهایی محصول کمک کنند.
- شفاف کننده های نانو (Nano-Clarifiers): تحقیقات در حال توسعه افزودنی های شفاف کننده در مقیاس نانو هستند. ذرات نانو به دلیل اندازه بسیار کوچکشان پتانسیل کاهش پراکندگی نور را حتی بیشتر از شفاف کننده های رایج دارند و می توانند شفافیت فوق العاده ای ایجاد کنند. این حوزه یکی از مرزهای جدید در فناوری افزودنی های پلیمری است.
انتخاب دقیق ترکیب افزودنی ها نیازمند درک عمیق از برهم کنش آن ها با پلیمر پایه و با یکدیگر است تا به خواص مطلوب (از جمله شفافیت) بدون تاثیر منفی بر سایر ویژگی ها دست یافت.
انتخاب افزودنی مناسب: چه عواملی را باید در نظر گرفت؟
انتخاب افزودنی مناسب برای بهبود شفافیت یک فرآیند پیچیده است که نیازمند در نظر گرفتن مجموعه ای از عوامل فنی اقتصادی و قانونی است. یک انتخاب نادرست نه تنها ممکن است به شفافیت مطلوب منجر نشود بلکه می تواند خواص دیگر پلیمر را نیز تحت تاثیر قرار دهد و یا هزینه های تولید را افزایش دهد.
برای اطمیناب از انتخاب بهینه لازم است سوالات کلیدی زیر را مطرح کرده و پاسخ های آن ها را با دقت بررسی کنیم:
- نوع پلیمر پایه چیست و ساختار آن (آمورف یا نیمه کریستالی) چگونه است؟
- دلیل اصلی کاهش شفافیت چیست؟ (ناسازگاری کریستالیزاسیون ناخالصی تخریب؟)
- چه فرآیندی برای تولید محصول استفاده می شود؟ (تزریق اکستروژن فیلم دمی؟)
- شرایط فرآیند (دما فشار زمان ماند) چگونه است؟
- کاربرد نهایی محصول چیست؟ (بسته بندی غذا قطعه صنعتی پزشکی؟)
- چه سطح شفافیتی مورد نیاز است؟ (کدورت (Haze) چند درصد؟)
- آیا محصول در معرض شرایط خاصی قرار می گیرد؟ (نور UV حرارت مواد شیمیایی؟)
- آیا الزامات قانونی یا استانداردهای خاصی (مانند تماس با غذا) برای محصول وجود دارد؟
- هزینه افزودنی و تاثیر آن بر هزینه نهایی محصول چقدر است؟
پاسخ به این سوالات به شما کمک می کند تا دایره انتخاب افزودنی ها را محدود کرده و گزینه های مناسب را شناسایی کنید. در ادامه به بررسی برخی از مهم ترین این عوامل می پردازیم.
سازگاری افزودنی با پلیمر پایه
مهم ترین عامل در انتخاب هر افزودنی سازگاری آن با پلیمر پایه است. افزودنی ناسازگار به خوبی در ماتریس پلیمری حل یا توزیع نمی شود و می تواند خود به عنوان یک ناخالصی عمل کرده و باعث کدورت شود.
سازگاری به معنای توانایی افزودنی در اختلاط یکنواخت و ماندن در پلیمر بدون مهاجرت یا جدایی فازی در طول زمان است. افزودنی های سازگار معمولاً ساختار شیمیایی مشابهی با پلیمر دارند یا دارای گروه های عاملی هستند که با زنجیره های پلیمری برهم کنش مناسبی برقرار می کنند. تست های آزمایشگاهی برای بررسی سازگاری (مانند تست های مهاجرت یا بررسی میکروسکوپی ساختار) قبل از استفاده در مقیاس تولید ضروری هستند.
تاثیر شرایط فرآیند بر عملکرد افزودنی
شرایط فرآیند تولید به خصوص دما فشار و زمان ماند مذاب پلیمری در دستگاه تاثیر بسزایی بر عملکرد افزودنی ها دارد. برخی افزودنی ها نسبت به دما حساس هستند و ممکن است در دماهای بالا تجزیه شوند یا خواص خود را از دست بدهند.
برای مثال برخی شفاف کننده ها یا آنتی اکسیدان ها ممکن است در دماهای فرآیند پلیمرهای با دمای ذوب بالا (مانند PET) پایداری کافی نداشته باشند و قبل از انجام وظیفه خود تخریب شوند. همچنین زمان ماند طولانی در دمای بالا می تواند به تخریب افزودنی و یا خود پلیمر منجر شود. بنابراین هنگام انتخاب افزودنی باید به محدوده دمایی فرآیند و پایداری حرارتی افزودنی در آن دما توجه ویژه داشت. تامین کنندگان افزودنی معمولاً اطلاعات دقیقی در مورد پایداری حرارتی محصولات خود ارائه می دهند.
تاثیر افزودنی بر سایر خواص پلیمر
افزودنی ها علاوه بر بهبود شفافیت ممکن است بر خواص دیگر پلیمر نیز تاثیر بگذارند. این تاثیرات می توانند مثبت یا منفی باشند.
برای مثال برخی نرم کننده ها می توانند مقاومت حرارتی یا مکانیکی پلیمر را کاهش دهند. برخی شفاف کننده ها ممکن است بر دمای ذوب یا سرعت کریستالیزاسیون تاثیر بگذارند. آنتی اکسیدان ها می توانند رنگ اولیه پلیمر را کمی تغییر دهند. بنابراین هنگام انتخاب افزودنی لازم است تاثیر آن بر کل مجموعه خواص مورد نیاز برای کاربرد نهایی مورد ارزیابی قرار گیرد. گاهی لازم است از ترکیبی از افزودنی ها استفاده شود تا به بهینه سازی همزمان چند خاصیت دست یافت.
الزامات قانونی و استانداردهای کاربردی
برای کاربردهای خاص مانند بسته بندی مواد غذایی تجهیزات پزشکی یا اسباب بازی الزامات قانونی و استانداردهای سخت گیرانه ای در مورد نوع و مقدار افزودنی های قابل استفاده وجود دارد. این استانداردها معمولاً توسط سازمان هایی مانند FDA در آمریکا اتحادیه اروپا (EU) یا سازمان های ملی در هر کشور تعیین می شوند.
اطمینان از انطباق افزودنی انتخابی با این الزامات برای سلامتی مصرف کننده و امکان عرضه محصول در بازارهای هدف بسیار حیاتی است. تامین کنندگان معتبر افزودنی معمولاً اطلاعات مربوط به انطباق محصولات خود با استانداردهای رایج را ارائه می دهند.
نکات کلیدی در استفاده از افزودنی ها برای بهبود شفافیت
صرف انتخاب افزودنی مناسب کافی نیست؛ نحوه استفاده از آن در فرآیند تولید نیز به همان اندازه اهمیت دارد. رعایت نکات کلیدی در فرآیندپذیری و ترکیب افزودنی می تواند تفاوت قابل توجهی در دستیابی به شفافیت مطلوب ایجاد کند.
- دوز مناسب: استفاده از مقدار بهینه افزودنی بسیار مهم است. مقدار کمتر از حد نیاز ممکن است تاثیر کافی نداشته باشد در حالی که مقدار بیشتر می تواند منجر به مشکلاتی مانند مهاجرت افزودنی به سطح کاهش خواص مکانیکی یا حتی افزایش کدورت شود. دوز بهینه معمولاً بر اساس آزمایشات و توصیه های تامین کننده افزودنی تعیین می شود.
- توزیع یکنواخت: افزودنی باید به طور کاملاً یکنواخت در سراسر ماتریس پلیمری توزیع شود. توزیع نامناسب می تواند منجر به نقاط با شفافیت متفاوت یا تجمع افزودنی شود که خود می تواند باعث کدورت موضعی شود. استفاده از تجهیزات اختلاط مناسب (مانند اکسترودرهای دوپیچه با طراحی مناسب پیچ) و تکنیک های صحیح بچینگ (مانند استفاده از مستربچ افزودنی) برای اطمینان از توزیع یکنواخت حیاتی است.
- شرایط فرآیند بهینه: دما فشار سرعت پیچ و زمان ماند در فرآیند تولید باید به گونه ای تنظیم شوند که افزودنی به طور کامل ذوب و توزیع شود اما از تخریب آن جلوگیری شود. به خصوص در مورد شفاف کننده ها پروفیل دمایی مناسب برای هسته زایی موثر کریستال ها در مرحله خنک کاری بسیار مهم است.
- کنترل رطوبت و آلودگی: رطوبت و آلودگی های دیگر در مواد اولیه یا در حین فرآیند می توانند بر عملکرد افزودنی ها تاثیر منفی گذاشته و باعث کاهش شفافیت شوند. خشک کردن مناسب مواد اولیه و حفظ محیط تولید تمیز برای جلوگیری از این مشکلات ضروری است.
- تست و ارزیابی: پس از تولید لازم است شفافیت محصول نهایی با استفاده از روش های استاندارد (مانند اندازه گیری کدورت و شفافیت با دستگاه Haze Meter) مورد ارزیابی قرار گیرد تا از دستیابی به خواص مطلوب اطمینان حاصل شود.
رعایت این نکات به شما کمک می کند تا از پتانسیل کامل افزودنی های بهبود دهنده شفافیت بهره مند شوید و محصولاتی با کیفیت و شفافیت بالا تولید کنید.
آینده افزودنی های بهبود دهنده شفافیت
صنعت پلیمر و افزودنی ها به طور مداوم در حال تکامل هستند و تحقیقات گسترده ای برای توسعه نسل جدیدی از افزودنی های بهبود دهنده شفافیت در حال انجام است. تمرکز اصلی این تحقیقات بر چند حوزه کلیدی است:
- کارایی بالاتر: توسعه افزودنی هایی که با دوز مصرفی کمتر بتوانند شفافیت بیشتری ایجاد کنند یا در طیف وسیع تری از پلیمرها و شرایط فرآیند موثر باشند.
- پایداری بهتر: بهبود پایداری حرارتی و نوری افزودنی ها برای استفاده در فرآیندهای با دمای بالاتر و کاربردهایی که در معرض شرایط محیطی سخت قرار دارند.
- سمیت کمتر و سازگاری با محیط زیست: توسعه افزودنی هایی که برای سلامت انسان و محیط زیست بی خطرتر باشند به خصوص برای کاربردهای تماس با غذا و پزشکی. جایگزینی افزودنی های بر پایه مواد شیمیایی بحث برانگیز با گزینه های سبزتر و پایدارتر.
- افزودنی های چندکاره: توسعه افزودنی هایی که همزمان چندین خاصیت را بهبود ببخشند مانند شفافیت همراه با پایداری حرارتی مقاومت در برابر خراش یا خواص ضد میکروبی. این افزودنی ها می توانند فرمولاسیون ها را ساده تر و هزینه ها را کاهش دهند.
- نانو افزودنی ها: همانطور که اشاره شد نانو ذرات پتانسیل بالایی برای بهبود شفافیت دارند. تحقیقات در حال بررسی استفاده از نانوذرات معدنی یا پلیمری به عنوان هسته زا یا عوامل سازگارکننده برای دستیابی به شفافیت فوق العاده و خواص مکانیکی بهبود یافته هستند.
این پیشرفت ها نویدبخش تولید محصولات پلیمری با شفافیت بی سابقه عملکرد بهتر و اثرات زیست محیطی کمتر در آینده هستند. فعالان این صنعت باید با پیگیری تحولات جدید از آخرین دستاوردهای این حوزه برای بهبود محصولات و فرآیندهای خود بهره ببرند.
خلاصه تر بخوانید
شفافیت در محصولات پلیمری، بهویژه در صنایع بستهبندی، پزشکی و خودروسازی، اهمیت بالایی دارد. کاهش شفافیت یا کدورت پلیمرها میتواند به دلایل مختلفی مانند ناسازگاری اجزا، وجود ناخالصیها، کریستالیزاسیون نامناسب و تخریب حرارتی یا نوری رخ دهد. هر یک از این عوامل باعث پراکندگی نور در ساختار پلیمر شده و ظاهر و عملکرد محصول را تحت تأثیر قرار میدهد.
برای رفع این مشکل، صنعت پلیمر از افزودنیهای تخصصی بهره میبرد. شفافکنندهها (Clarifiers) مهمترین افزودنیها برای پلیمرهای نیمهکریستالی مانند پلیپروپیلن و پلیاتیلن هستند. این مواد با کنترل فرآیند کریستالیزاسیون، اندازه کریستالها را کاهش داده و پراکندگی نور را به حداقل میرسانند. مشتقات سوربیتول و مواد معدنی هستهزا از رایجترین شفافکنندهها محسوب میشوند.
نرمکنندهها (Plasticizers) نیز با افزایش سازگاری اجزا و کاهش تنشهای داخلی، میتوانند به بهبود شفافیت کمک کنند، هرچند نقش اصلی آنها افزایش انعطافپذیری است. آنتیاکسیدانها و پایدارکنندههای UV با جلوگیری از تخریب حرارتی و نوری، مانع زردشدگی و کاهش شفافیت میشوند. همچنین عوامل سازگارکننده و افزودنیهای نانو نیز در بهبود شفافیت نقش دارند.
انتخاب صحیح افزودنیها باید با توجه به نوع پلیمر، فرآیند تولید، کاربرد نهایی، شرایط محیطی و الزامات قانونی صورت گیرد. همچنین دوز مناسب و توزیع یکنواخت افزودنیها در ماتریس پلیمری اهمیت زیادی دارد. شرکت بازرگانی شیمی سنتر فروشنده مواد اولیه صنعت، با ارائه افزودنیهای تخصصی و باکیفیت، میتواند نقش مهمی در بهبود شفافیت و کیفیت محصولات پلیمری ایفا کند و به تولیدکنندگان در دستیابی به استانداردهای جهانی کمک نماید.
چه مقدار افزودنی برای بهبود شفافیت پلیمر لازم است؟
مقدار دقیق افزودنی به نوع پلیمر نوع افزودنی سطح شفافیت مورد نیاز و شرایط فرآیند بستگی دارد. معمولاً دوز مصرفی شفاف کننده ها بسیار کم و در حد 0.1 تا 0.5 درصد وزنی است. دوز نرم کننده ها می تواند بسیار بالاتر باشد. همیشه به توصیه های تامین کننده افزودنی مراجعه کنید.
آیا استفاده از افزودنی ها بر خواص مکانیکی پلیمر تاثیر می گذارد؟
بله افزودنی ها می توانند بر خواص مکانیکی تاثیر بگذارند. شفاف کننده ها معمولاً تاثیر کمی دارند یا حتی ممکن است سختی را کمی افزایش دهند. نرم کننده ها انعطاف پذیری را افزایش و سختی را کاهش می دهند. آنتی اکسیدان ها معمولاً تاثیر مستقیمی بر خواص مکانیکی ندارند اما با جلوگیری از تخریب به حفظ خواص در طول زمان کمک می کنند.
چگونه می توانم از توزیع یکنواخت افزودنی در پلیمر اطمینان حاصل کنم؟
استفاده از تجهیزات اختلاط مناسب مانند اکسترودرهای دوپیچه انتخاب فرم مناسب افزودنی (مانند پودر ریز یا مستربچ با کیفیت) و تنظیم بهینه پارامترهای فرآیند (دما سرعت پیچ) برای اطمینان از ذوب و توزیع کامل افزودنی در مذاب پلیمری ضروری است.
آیا افزودنی های بهبود دهنده شفافیت برای استفاده در تماس با مواد غذایی مناسب هستند؟
خیر همه افزودنی ها برای تماس با مواد غذایی مناسب نیستند. افزودنی هایی که در محصولات تماس با غذا استفاده می شوند باید دارای تاییدیه و گواهینامه های لازم از سازمان های نظارتی مانند FDA یا اتحادیه اروپا باشند. همیشه از تامین کننده افزودنی مستندات مربوط به انطباق با استانداردهای غذایی را درخواست کنید.
بهترین روش برای آزمایش شفافیت پلیمر چیست؟
بهترین روش برای آزمایش شفافیت استفاده از دستگاه Haze Meter است که میزان کدورت (Haze) و شفافیت (Clarity) نمونه پلیمری را بر اساس استانداردهای بین المللی (مانند ASTM D1003) اندازه گیری می کند. این روش نتایج کمی و دقیقی ارائه می دهد.